Finite capacity scheduling enables you to manage and maintain a production schedule efficiently. It helps with sequencing production orders on your machine and work centers and ensures you use your capacities wisely.
However, we all know that things seldom go as planned. Material arrives later than expected. Or it is there but cannot be used due to quality issues. A machine breaks. Your machine operator figures out that he has to run the machine slower than planned. Just to name a few incidents that can make your well-defined schedule obsolete every moment.
Two weeks ago, our CEO Martin held a webinar showing how you, as a production planner, can rapidly react to these incidents. He demonstrated the newly implemented integration with shop floor data of the latest VAPS version that lets you identify deviations from actual versus plan immediately and with which you can update your schedule on the fly - so that it is always current.
Read this blog to get a written wrap-up of the webinar with links to the respective minute of the presentation. At the bottom of the page, you'll find the link to the recorded webinar on YouTube.
Martin dived into his topic by describing one of the key problems in production scheduling: on the one hand, you have your schedule, and on the other hand, there's the reality on your shop floor.
A data gap in Business Central [min 3:20]
In terms of Busines Central, this could be (a bit simplified) described as a gap between data concerning production scheduling (plan data) and data concerning the production progress (actuals).
The "Chinese Wall" in Business Central [min 5:22]
Martin went on by stating that there is a kind of a "Chinese Wall" between the production order routing lines and the capacity ledger entries in that there is no data feedback from the shop floor to the planning. The two tables are completely separated, and it doesn't matter what you post in the capacity ledger entries - it will not impact the production order routing lines.
Implications of the "Chinese Wall" - example [min 6:52]
Of course, the above-described missing communication between the two tables can create some issues, as is shown by the below example:
-
A production order is scheduled for machine 1.
-
The machine operator starts it on machine 2 and posts it accordingly.
-
The capacity ledger entry says: „The production order was started on machine 2“.
-
The routing remains unchanged.
-
The planner still sees the production order according to the routing on machine 1 (although everybody knows it runs on machine 2)
-
Implications of the "Chinese Wall" - what Business Central allows [min 9:34]
Martin stated that there are almost no logical checks when it comes to capacity ledger entries and postings and illustrated this by listing some of the actions that are allowed in Business Central - some quite advantageous and others with negative effects:
- One operation can be posted on several different machines
- Partial quantity 1: machine 1
- partial quantity 2: machine 2
- Operations are started and stopped in a revolving manner
- Start production order 1 on machine 1
- stop production order 1 on machine 1
- start production order 2 on machine 1
- stop production order 2 on machine 1
- Start production order 1 on machine 1
- The end date can be posted before the start date
- Posting on a machine that is not allowed / feasible
- Posting – after the fact – on an already finished production order
Possible deviations between plan and actuals [min 12:22]
Based on the postings being possible in standard Business Central, the following deviations between the plan and the actuals can occur:
-
Deviation in resource
= an operation gets started on a different work/machine center than specified in the routing (referred to the most recent posting) -
Deviation in duration
= the posted setup time and/or run time differs from the corresponding time in the routing (differs à is larger than) -
Deviation in time
= the posted start time and/or the posted end time differs from the corresponding time in the routing (if time is posted; else: date) -
Deviation in quantity
= the posted quantity differs from the planned quantity (differs à is larger than)
How the VAPS deals with plan/actual deviations (min 18:01]
Martin then explained the three steps the VAPS follows when dealing with the deviations described above:
Step 1: Identify plan/actual deviations.
- Load new shop floor data
- New color scheme "Shop Floor Status"
The standard color settings in the color scheme indicate the deviations as follows:
Step 2: Update simulation with actuals.
The operations get rescheduled based on the actuals. This happens as follows:
-
The operations get the posted starting date/time
-
If the actual time (duration and/or timing) differs from the planned time, the length of the bars gets changed accordingly (if the time was prolonged)
This, of course, has certain implications for the planned operations:
-
An operation gets prolonged due to shop floor postings: all predecessors on that machine (and their predecessors on other machines) are automatically moved to the right
-
An operation gets shortened due to shop floor postings: we do not automatically change the plan (de facto, this should not happen anyway. We can only tell after the „finish“ posting if the operation WAS shorter than planned. Before the „finish“ posting, we only have „in progress“ information).
-
Two options to handle this case:
-
The operator starts the next waiting operation anyway. By this, this operation gets a new starting date in the VAPS, and the changes will get reflected.
-
You see a gap in the schedule, which you can fill with the VAPS tools.
-
-
In the VAPS, you can update your plan with shopfloor as shown below:
- For the entire schedule at once: from menu
- For a single production order routing line: right click
What is more, for you to monitor all these changes and to get a better grip on the actuals, we redesigned the dateline:
Step 3: Publish the simulation.
Don't forget to publish your simulation because only then will the changed routing information get written back to the Business Central routing lines.
Live demo [min 31:50]
All theory was then put into practice, and Martin gave a vivid presentation of how easily and conveniently the VAPS manages the integration of the shop floor data into the plan.
Click here, to watch the webinar on YouTube. And don't forget: we are always glad to see and hear you in an upcoming webinar or event. Check out our webinar and events calendar.
Want to dig still deeper?
- Watch more recorded introductory and in-depth webinars about visual production scheduling in Business Central
- Book a free demo with a VAPS specialist
- Get your free copy of our comprehensive eBook:
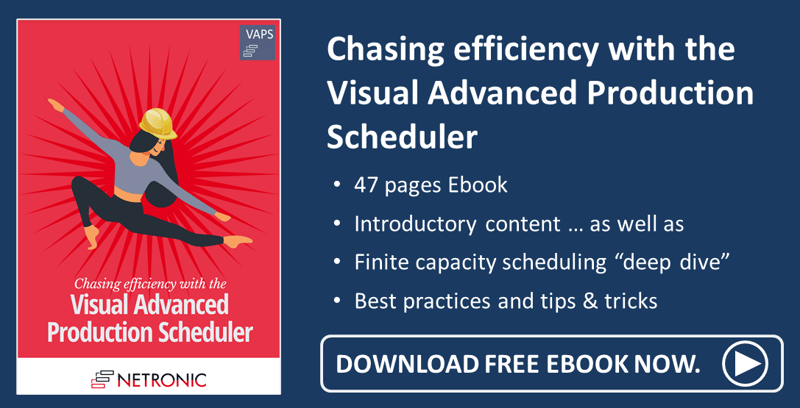