Planners do not want reservations between production orders and sales orders to break if production delays occur. Instead, they want to quickly understand which sales orders run late due to material and/or capacity constraints. To solve these problems, the latest VAPS version comes with an enhanced and improved integration of sales orders and production orders. As promised in his webinar on this release, our CEO Martin held an in-depth webinar on this very topic some weeks ago.
Read this blog to get a written wrap-up of the webinar with links to the respective minute of the presentation. At the bottom of the page, you'll find the link to the recorded webinar on YouTube.
After some introductory words, Martin explained what the webinar would be about and who should watch it.
The target audience of the webinar [min 3:07]
The contents of this webinar are meant for partners working with manufacturing clients or for manufacturers
-
who produce to order (at least, where the final product is made for a concrete customer)
-
and who somehow wish there would be a bit more flexibility in the reservation system
-
Especially when it comes to reserving production orders for sales orders - other reservations are not dealt with in this session
Or in other words
The reservation system as described by Microsoft [min 6:44]
Martin explained that the reservation system of Business Central provides customers with clear visibility of the network between supply and demand and that this ability is one of the system's very strong selling points.
He then went into how the reservation system is explained in the Microsoft documentation, like shown in the list below.
As he stated, the last statement makes him slightly concerned because, ultimately, a powerful system like Business Central should naturally try to reduce manual work.
- The reservations system is comprehensive.
- At the core of the reservation system is the linking of a demand entry and a corresponding supply entry.
- A reservation is a firm link that connects a specific demand and a specific supply to each other
- A reservation is a user-generated link, and an order tracking record is a system-generated link
-
When a user intentionally creates a reservation, the user gains full ownership of and responsibility for these items. This means that the user must also manually change or cancel a reservation. Such manual changes may cause automatic modification of the involved reservations.
From here, Martin led over to a short explanation of when automatic reservations are triggered in Business Central at all.
Automatic reservations [min 10:24]
-
The item card can be set up to always be reserved automatically from demand, such as sales orders.
-
Items are automatically reserved by various planning functions to keep a demand linked to a specific supply.
-
This happens in the following cases:
-
A multilevel production order where the manufacturing policy field of the involved parent and child items is set to make-to-order.
-
A production, assembly, or purchase order where the reordering policy field of the involved item is set to order.
-
A production order created from a sales order with the sales order planning function is linked to the sales order with an automatic reservation.
-
An assembly order is created automatically for a sales order line to fulfill the quantity in the “qty. to assemble to order” field.
-
Special features in the manual reservation that require further investigation [min 11:25]
While researching the reservation system, Martin came across a table that only exists for manual reservations and lists when and which modifications may occur. The picture below only shows the modifications - either on the supply or the demand document - that are relevant to our topic:
For Martin, the following conclusions and questions have arisen from this:
-
The fact that this table only exists for manual reservations suggests the assumption that a similar table is not provided for automatic reservations, and from this, one could conclude that the red-marked case ("reservation canceled") does not occur with automatic reservations.
-
Do users get notified if a reservation is canceled for a manual reservation?
Live demo: How reservations behave if date fields are changed [min 13:21]
Switching to the VAPS, Martin tested different cases of changing either the sales orders (demand) or the production orders (supply). Doing so, he discovered that the Microsoft documentation is not quite correct at this point because, as he showed, there is no difference between making reservations between production orders and sales orders manually or automatically. When a situation arises where you either need the delivery from your sales order earlier than the production order is planned to be finished or if you move the production order to a date after the shipment date from the sales order, you always get a warning and can decide whether you let Business Central delete the reservation or whether you delete the reservation manually in one document and then update the other accordingly. However, you should not forget to make a new reservation in both cases.
Martin put the different cases and their impacts together in a descriptive overview:
Summary: Changes to date fields
Business Central reservation system is a superpower - but ... [min 22:25]
It is really great that Business Central makes sure to keep the link between the demand of the sales order and the supply of the production order valid and in balance, but Martin's long-term experience has shown him that the system is built on sand to a certain degree, especially when it comes to production orders and sales orders.
What is the sand that reservations are built upon? [min 24:04]
Martin supported his thesis with the following graphic:
Live demo: Get more meaningful information about capacity issues than provided by Business Central
[min 29:12]
In this section, Martin showed that it is very hard to find out where you have your capacity issues. Also, in a task list that still contains comparatively few entries, an overloaded machine center can't be detected too easily, even when the list is filtered. In the below picture, you have to look really hard to recognize that the firm planned production order doesn't make sense because it is just in the middle of the other two.
What is more, the steps needed to clean this up are extensive and cumbersome and, as lots of customers have told us, lead to frustration.
Production scheduling software working with or against Business Central? [min 34:24]
Trying to find a solution for the above-described dilemma, Martin pointed out two options and their pros and cons:
-
Option 1: Production scheduling software can work with Business Central
- The software understands Business Central
- It understands reservations
- It understands reservations as a restriction
- Hence, it will not violate reservations
- Customers are back where they were before and need to manage the reservation system (manually)
- But they bought additional software (that does not solve the issue)
-
Option 2: Production scheduling software can work “against” Business Central
- The software schedules (against finite capacity)
- Production orders change
- Production orders get later than requested by the due date (from the sales order)
- The scheduling software pretends to “know better” than Business Central
- It saves the changes to the production orders (and silently “kills” the reservations)
- Problem solved?
- Yes, if customers do not need to see which production order serves which sales order
-
And yes, if customers do not work with the planning worksheet (which otherwise would observe and correct an imbalance between demand and supply)
The above comparison showed that neither option is suitable for cutting the Gordian Knot.
So, what do customers need? [min 37:47]
Coming back to the shock absorber mentioned at the beginning, Martin identified the functionality a production software should offer to deal with the reservation issue satisfactorily:
-
Planners need to be able to track the link from production orders to sales orders (and vice versa).
-
This link must be kept when production orders move due to finite capacity.
-
Sales want to see which orders are later than initially planned.
How we made this happen in the VAPS [min 38:57]
As Martin related, our development team had been thinking about an appropriate approach for some time when he met Matthes Schubert from SHB Business Solutions, who had a solution for the problem and thankfully shared it with us. The way the VAPS now works with reservations can be best described by the picture below:
Live: How the VAPS handles reservations and notifies the user of changes [min 42:26]
In the last live demo of the webinar, Martin showed how easily and conveniently the VAPS allows changes to the orders while keeping the reservations and, on top of that, provides a comprehensive and clear report on the changes made.
I hope I whet your appetite for watching this webinar. And, of course, we are always glad to see and hear you in an upcoming webinar or event. Check out our webinar and events calendar.
Want to dig still deeper?
- Watch more recorded introductory and in-depth webinars about visual production scheduling in Business Central
- Book a free demo with a VAPS specialist
- Get your free copy of our comprehensive eBook:
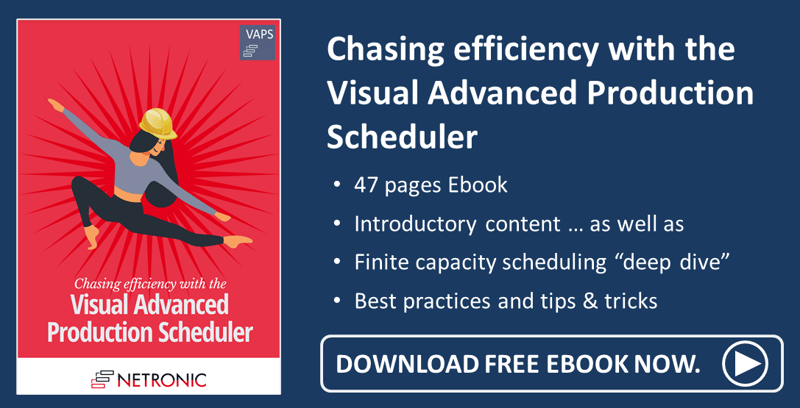